|
By Rhoda Miel STAFF REPORTER Published: August 22, 2013 2:10 pm ET
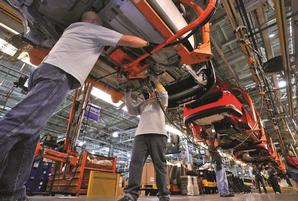
Image By: Ford Motor Co. At Ford's Michigan assembly plant, employees attach a charger to a Focus Electric, one of five vehicles built at the facility
TRAVERSE CITY, MICH. — The good news for the North American auto industry is that vehicle production is not only up, but the expectation is that production will continue to increase during the coming years. That's also the — well, if not bad news, then certainly concerning news. A North American supply base that cut back during the recession is now stretching the upper limits of its current capacity. Scott Kunselman, senior vice president of purchasing and supply quality at Chrysler Group LLC, termed the industry as being at "hyper utilization" during the Center for Automotive Research's Management Briefing Seminars, held Aug. 5-8 in Traverse City. Large-tonnage injection molding presses are especially at a premium right now, according to one auto industry insider, while automakers and top suppliers alike are looking all along the supply chain to try to make certain that a problem in one region or at one small company will not slow production for everyone. "We're looking down that supply chain to the Tier 2, 3 and 4 companies and doing our own assessments on those suppliers," said Bill Wardle, global vice president of sales and marketing for interiors, exteriors and seating at Magna International Inc. of Aurora, Ontario. "We want to make sure that one particular widget isn't being sourced to one company in Toledo, for instance, that would end up being a bottleneck for everyone." It's been a radical shift for the auto industry. In the early 2000s, the North American industry was growing rapidly, with new production coming on line. Then came the recession and bankruptcies at both Auburn Hills, Mich.-based Chrysler and General Motors Co. Within one year, vehicle output fell to less than 9 million vehicles from more than 16 million. Many companies shut down plants, took presses off line and cut employment just to survive. Some small firms quietly went out of business. Nearly new presses sold on the auction block for a fraction of their original cost. But this year, forecasters predict production levels will bounce back to between 15.5 million and 16 million vehicles, and expect that number to climb above 16 million in the next few years. The North American auto industry added 600,000 vehicles to the production base in 2012 and 2013, said Birgit Behrendt, vice president of global programs and purchasing operations for Dearborn, Mich.-based Ford Motor Co. Ford's Brownstown Township plant is up to three shifts a day, six days a week. Nissan Motor Co. is running the bulk of its North American plants six days a week, taking a day off just to keep machines in good condition. "That Sunday off is really required to maintain all of the equipment when you're running as heavily as we've been doing," said Bill Krueger, senior vice president of manufacturing, purchasing, production engineering and supply chain management for Nissan Americas. Memories of the 2009 crash are fresh, though, and many suppliers are wary of putting a lot of money into expansions. The base has a "conservative capacity mindset," Behrendt said. Ford met with its top 100 suppliers in June to discuss its needs for capacity in the coming years, she said. One new press can easily top a $1 million investment including auxiliary equipment, but the traditional domestic automakers typically have not been willing to provide long-term business guarantees, said Laurie Harbour, president and CEO of consulting group Harbour Results Inc. Toolmakers also have to contend with a business cycle that varies throughout the year, with peaks that push the limits of their capacity just prior to a new vehicle launch and valleys that make it hard to find enough business to keep both equipment and people busy, she said. A survey from the Original Equipment Suppliers Association this year indicated that companies are adding employees and equipment, but are reluctant to build new plants or expand existing ones, said David Andrea, OESA's senior vice president of industry analysis. Magna has been an exception. It recently began building two plastics facilities in Michigan — in the Lansing suburb of Delta Township and in the Detroit suburb of Browns¬town Township — spending $81.75 million on new injection molding, painting and assembly lines and another $162 million to be spent on a die-casting facility in Battle Creek, Mich. Wardle noted, though, that the firm was very cautious before committing to that expansion. "During the downturn, we never really took fixed assets out of production. We cut shifts and we put [equipment] into mothballs, but we're just now getting to the point where we're starting to add capacity," he said. The difference is that the North American production has reached a "tipping point" of building 16 million vehicles, Wardle said. That creates the critical mass needed to support new capital equipment investments. Even looking at that total production number does not mean that the company will invest, though. "I've been around this industry for over 20 years and I know that the scrutiny we go through now to get a couple of million [dollars for capital equipment] is tenfold from where we were before," he said. "We're a lot more diligent about adding capacity because ... we all know what it was like in 2009." Improvements in automation and technology have also allowed companies including Magna to get more out of existing equipment. The overall manufacturing number is just one statistic. Within that, the figures break down much more. One vehicle projected to sell 300,000 units per year may fall far short of that, while another that is expected to sell 70,000 may exceed forecasts by 20-30 percent. Suppliers need to be able to shift equipment or people to keep up with reality. Capacity concerns in North America are not global issues, however. The struggling auto industry in Europe has led to excess capacity there with some companies shutting down plants. China is continuing to grow but at a slower rate than in the past. Big parts cannot easily be sourced from available capacity in Europe, which leads back to worries about shortages in the U.S., Canada and Mexico. To help encourage investments, automakers are working to lock in commitments from their key suppliers while also giving them some assurances of future work. Ford is paring down its list of global suppliers from more than 2,500 in 2006 to a goal of 750, Behrendt said. Those who number in the final group will jointly represent 65 percent of Ford's purchasing. Chrysler and Detroit-based GM are doing the same, looking to lock in capacity needs for the coming years.
| |