|
By Rhoda Miel STAFF REPORTER Published: August 19, 2013 2:12 pm ET
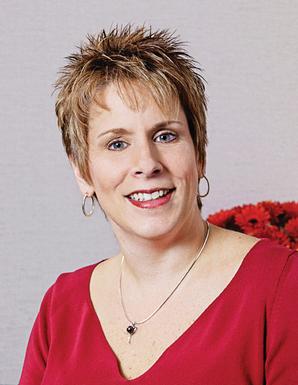
TRAVERSE CITY, MICH. — Ford Motor Co. is in the midst of a hiring blitz, planning to add a total of 6,200 hourly employees and 3,000 salaried workers in the U.S. within two years to keep up with an expanding consumer demand. Other automakers have also been adding jobs at factories and offices. With unemployment nationally topping 8 percent, it seems like it would be easy to fill those jobs, but Ford's Jim Tetreault, vice president North America manufacturing, said hiring is far more complex. For every job it fills, the company interviews 30 candidates on average, trying to find the right person. "We look at what candidates can do as well as what they will do," Tetreault said during the Center for Automotive Research's Management Briefing Seminars, held Aug. 5-8 in Traverse City. "Factors associated with motivation — work ethic, conscientiousness and teamwork — are just as important in an effective employee as skills and abilities such as reading, arithmetic, defect spotting and manual assembly." Which raises a whole new question for Laurie Harbour, president and CEO of consulting group Harbour Results Inc.: If a company like Ford has problems finding good employees, what does that say for a small company in the supply base without the reach or pay levels of an auto¬maker? It's a question echoed by companies throughout the supply chain that are not only trying to fill existing manufacturing spots, but also recruit the next generation of skilled workers. "We are not developing our [new] people soon enough, and it is extremely hard to find the right people," said David Grimmer, president of Kariya, Japan-based Denso Corp.'s Canadian operations. It seems difficult to believe that the same industry that slashed jobs just five years ago now finds itself with staff shortages. Michigan alone lost 50 percent of its manufacturing jobs in 2008, Grimmer noted. But once their jobs were cut, qualified workers who were discouraged when the auto industry collapsed sought work in other fields. They are not interested in even applying for posts with automakers and suppliers now. Harbour noted their absence is creating a void in the middle of the employment pack. Many suppliers were able to retain their veterans through the downturn, and have now started hiring new workers. But there are not enough workers today who are in the late 20s or early 30s, the people who would be mentors to the newest generation of skilled laborers. "We are really struggling with middle management," said Staci Kroon, automotive president for the North American division of Eaton Corp. of Cleveland, Ohio. "They left in 2008 and 2009 and we're struggling to try and get them back." The U.S. also suffers in comparison with competitive companies in Japan and in Europe, where schools have an education track specifically targeted to skilled trades. "A production job is not seen as glamorous and sought-after," Grimmer said. "How do we change that?" If schools are encouraging students to go into manufacturing, then manufacturers must begin outreach programs themselves by sponsoring visits, supporting robotics teams or getting the word out about computer-aided design/engineering. "Go after the kids when they're 12, 13, 14, 15, 16 years old," he said. Once companies find those workers, though, they must continually develop skills. Ford is working on new skilled-trades programs specifically geared toward the people who will build hybrid and electric-powered vehicles, Tetreault said. Chrysler Group LLC has created the World Class Manufacturing Academy, housed in a United Auto Workers building, to troubleshoot new production and "micro-stoppages," which slow existing production lines. Chrysler has a similar process — WCM-Light — to set up the same training for suppliers who may need extra focus. Motion-capture technology is used at Chrysler, Ford, Nissan and other auto assembly plants to build on manufacturing skills. Semi-skilled workers at Ford receive up to six months of training in simulated factories before they hit the production lines, and skilled workers see up to nine months in training before a new product launch, with the automaker expanding that training level to plants globally, Tetreault said. The training programs not only help to smooth out production issues, they improve quality and reduce injuries related to ergonomic issues, he said. | |